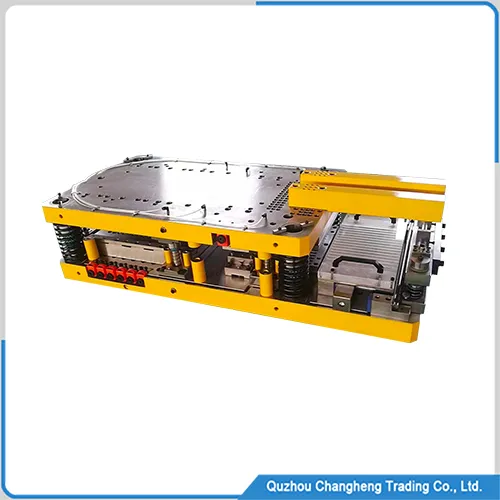
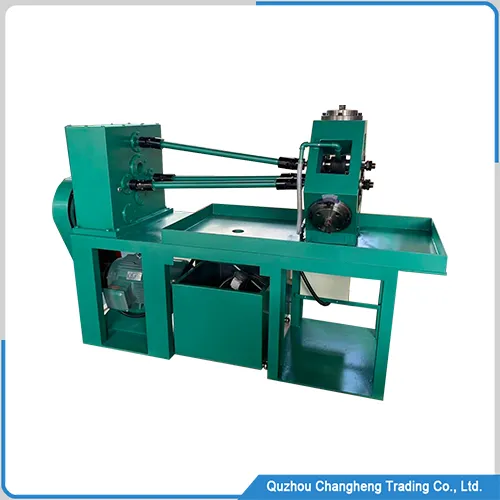
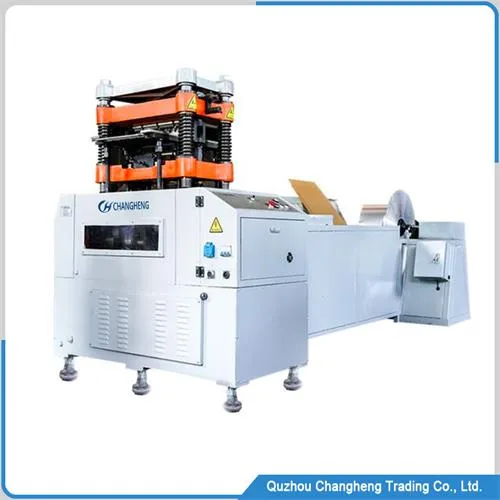
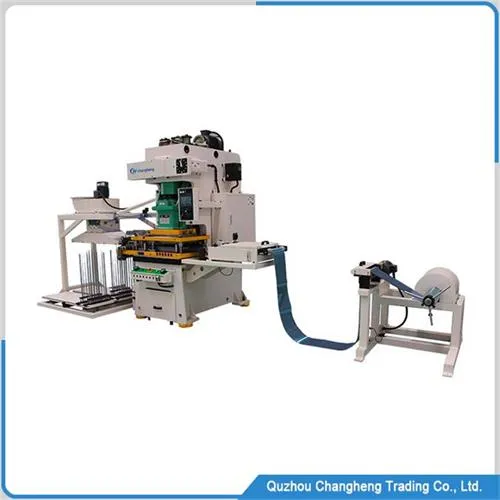
Progressive die, which is composed of multiple units, each unit completes different work in sequence and completes a series of different stamping processes in one stroke of the punch. Its other name is a continuous stamping die.
Working principle
A progressive die (also known as continuous die) comprises multiple stations; each station completes different processing sequences and a series of different stamping processing in one punch stroke. After a stroke is completed, the material is moved forward by the punch feeder according to a fixed step distance so that multiple processes can be completed on a pair of dies, generally including punching, blanking, bending, edge cutting, deep drawing, etc.
Features
- The progressive die is a multi-task sequential die. In one die, it can include multiple processes such as blanking, bending, forming, and stretching, with high productivity;
- Safe operation of progressive die;
- Easy to automate;
- High-speed punches can be used for production;
- It can reduce the area of the punch and site, as well as the transportation of semi-finished products and warehouse occupation.
- Parts with highly high dimensional requirements should not be produced with a progressive die.
Design requirements
- The parts are small;
- Large batch;
- The material is thin (0.08 ~ 2.5mm);
- The material is soft;
- Complex shape;
- Precious metals are not suitable (low utilization);
- The accuracy should not be too high (below 10)
Application of progressive die
The following aspects should be considered if a stamping part adopts a multi-station continuous die:
Design, manufacture and maintenance
The structure of the multi-station continuous die is quite complex, and the manufacturing accuracy is much higher than that of the general die. After each batch production, it must be overhauled and sharpened once and can only be put into storage for use after passing the test punching. Some small punches must be replaced after the inserts are worn or damaged. For the multi-station continuous die of bending, drawing, and forming, the relative height of other parts shall be corrected when grinding the edge of the punch and die. For multi-station continuous dies for bending, deep drawing, and forming, the heights of male and female dies are often different, so the relative difference required by the original design must be maintained after grinding. There must be a certain level of technical maintenance workers and more sophisticated special equipment.
Applicable press
The press used for the progressive die shall have sufficient strength, rigidity, power, and accuracy, a large working table, and a reliable braking system. The stroke of the punch should not be too large to ensure that the guide system of the die base of the continuous die is not disconnected during operation. Generally, the work shall be carried out under 80% of the nominal pressure of the press. The multi-station progressive die shall have a detection mechanism for strip feeding failure. After the detection mechanism sends a signal, the braking system must be able to stop the press immediately to avoid damaging the die or machine tool.
Good processed materials
During the stamping process of the progressive die, intermediate annealing is not allowed, which makes it difficult to add lubrication during processing.
Therefore, the mechanical properties of stamping materials must be relatively stable, and each batch of materials entering the factory must be tested and inspected according to the regulations; Progressive die stamping has higher requirements on the width and thickness tolerance of the strip used, as well as the flatness of the edge of the strip, because they will directly affect the stamping effect and the feeding of the strip.
Stamping parts should be suitable for progressive die production
- The output and batch of processed parts shall be large enough.
- The material performance of the multi-station continuous die is lower than that of other dies.
- The feeding accuracy and the cumulative error between each step will not reduce the part accuracy.
- The multi-station continuous die is ideal for parts with complex shapes that are difficult to locate after punching.