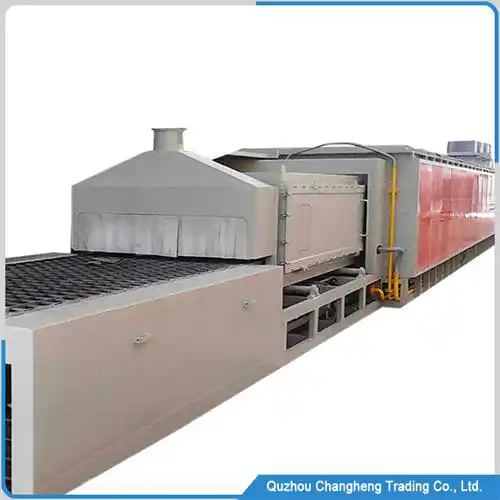
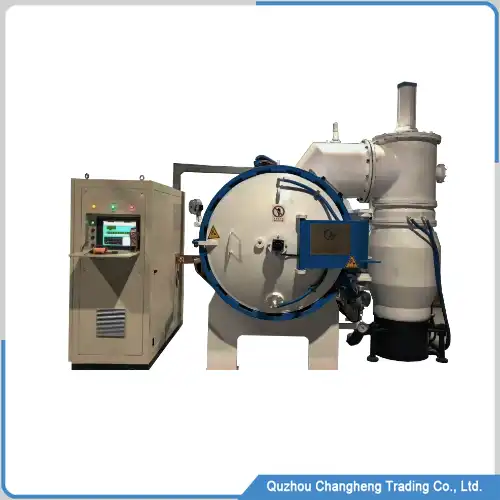
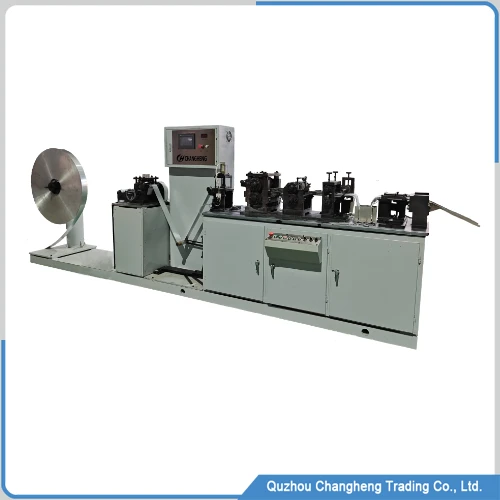
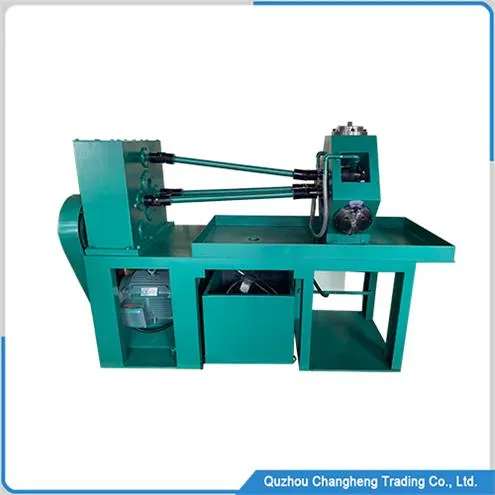
Machine Overview
The Tunnel brazing oven is the equipment used for continuous production of aluminum condensers. The device adopts a tunnel-type mafu structure,
Can achieve continuous production processes such as drying, brazing, and cooling of aluminum materials, applied in large-scale aluminum radiator and condenser factories
Tunnel Brazing Oven Features
1, Uniform heating:
Using tunnel heating can achieve uniform heating of the entire aluminum material, avoiding local high or low temperatures and ensuring the stability of brazing quality.
2, High production efficiency:
By adopting a continuous production line, continuous production can be achieved with high production efficiency, which can meet the needs of large-scale production.
3, Energy conservation and environmental protection:
By adopting advanced heating technology and control systems, energy conservation and environmental protection can be achieved, which is in line with the development trend of modern manufacturing industry.
4, Safe and reliable:
The equipment adopts multiple safety protection measures, such as temperature sensors, pressure sensors, leakage protection, etc., to ensure the safety and reliability of production.
Tunnel brazing oven data
No. | ITEM | DATA |
1 | Appearance | 100% NEW |
2 | Width | 1.85m |
3 | Length | 32m |
4 | Weight | 23T |
5 | Nitrogen | 40-65 m3/h |
6 | Transmission chain | china brand |
7 | Power | 280KW |
control system
The 10.1-inch touchscreen control system of this Tunnel Brazing Oven is a human-computer interaction interface that can achieve automated control and monitoring of the device. It has the following advantages
1) User friendly interface:
Adopting a user-friendly interface design, the operation is simple and easy to understand, and real-time control and monitoring of the production process can be achieved. And comes with two languages to choose from
2) Multiple control methods:
The Tunnel Brazing Oven It can be controlled through various methods such as touch screen, PLC, PC, etc., to meet different production needs.
3) Multiple parameter settings:
heating temperature, insulation time, brazing time, and other parameters can be set to ensure the stability and controllability of the production process.
4) Data recording and analysis:
It can record various data during the production process, such as temperature, pressure, time, etc., and conduct data analysis to provide data support for production optimization and quality control.