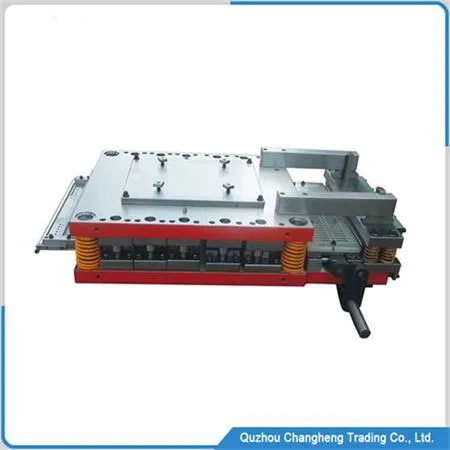
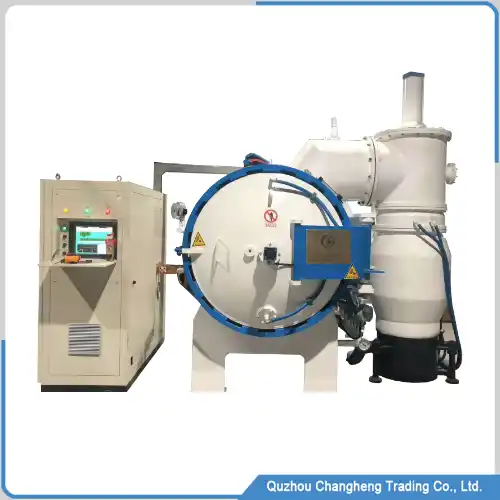
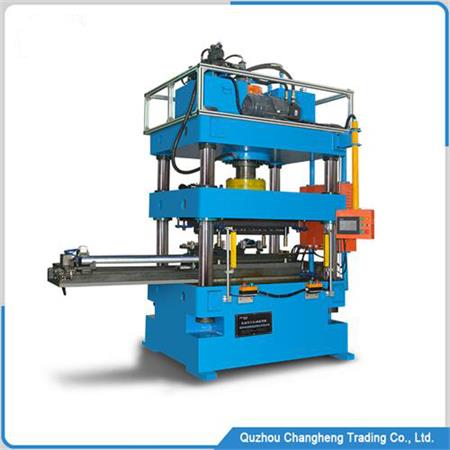
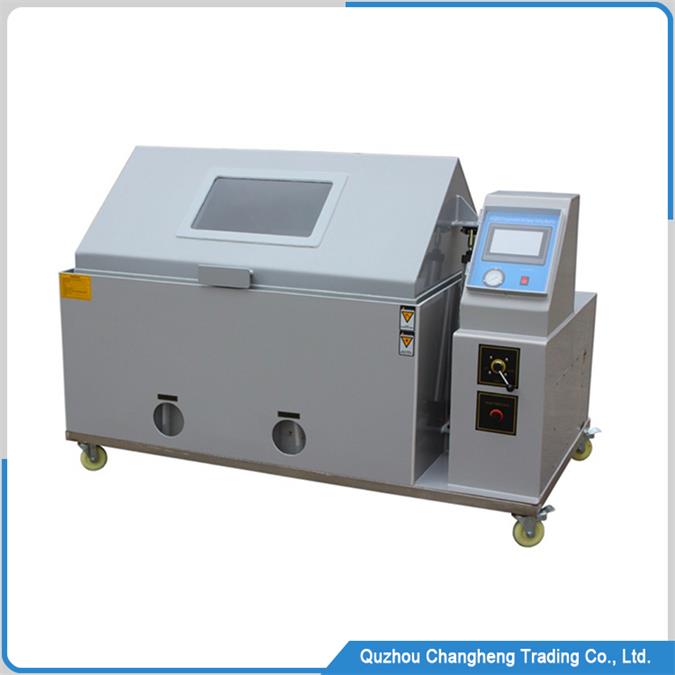
Press mold Overview
As a Chinese manufacturer of fin press dies, we provide customized solutions, design and manufacturing, testing, and maintenance services to meet our customers’ unique needs.
Our mold design is unique, with key components adopting independent structural design. When they wear out, they can be replaced at a low cost. This design not only significantly increases the mold’s service life but also effectively guarantees the quality of the heat exchanger’s fins.
Whether you are in the refrigeration industry, air conditioning industry, or automotive radiator industry, our fin molds can provide the best solutions and competitive costs.
Fin press die data
No. | ITEM | DATA |
1 | hole rows | based on geometry |
2 | Foil thickness | 0.05-0.5mm |
3 | Materials | aluminum copper Stainless Steel |
4 | Enhancements | Louwered – Lance |
5 | Collar height | 1.5-12mm |
6 | Fin Edge | Plane Corrugated |
7 | Fin length | freely controlled |
8 | hole diameter | customized |
Advantage of fin mold
1, High production efficiency:
The fin progressive die adopts a continuous automatic production method, which can be pressed 280 times per minute, resulting in high production efficiency
2, High precision:
Because CNC machine tools process all mold parts, ensuring the accuracy of all dimensions and shapes
3, Material saving:
During the production process of the fin press die for fins, the material utilization rate is high and there is almost no waste of raw materials
4, Reduce labor intensity:
The production process of fin progressive molds is automated, and the entire production process does not require manual intervention
5, Suitable for large-scale production:
Fin press dies are suitable for large-scale production and can reduce production costs.
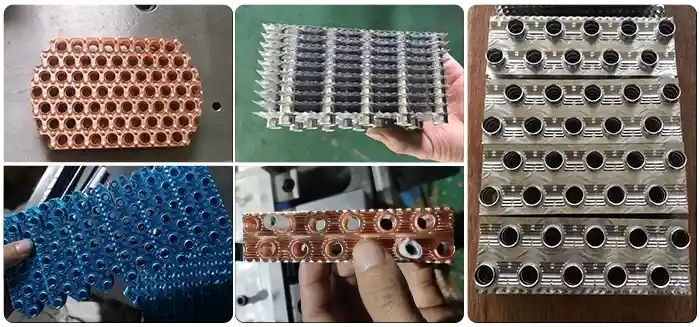
WHY CHOOSE US
With the continuous advancement of technology and the growing demand for energy conservation, the shape of fins has become increasingly diverse, and tolerances have become stricter.
We have chosen an integrated mold design scheme; CNC machining completes the entire template to meet strict tolerance requirements.
Reasonable structural design has increased heat transfer efficiency by 12%.
The fin mold adopts multiple distributed stretching designs and can produce a maximum collar height of 15mm.
The key components of the mold are all treated using heat treatment technology, and the mold’s entire service life exceeds 400 million presses.