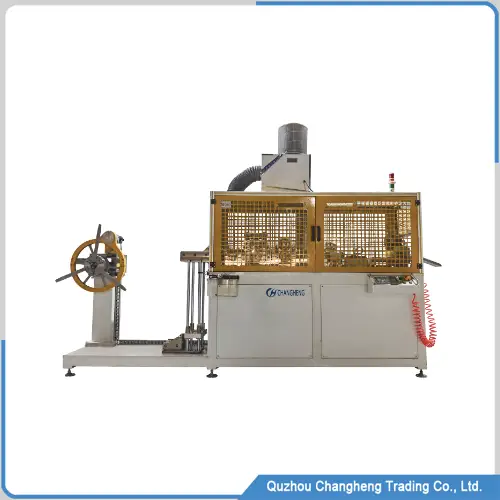
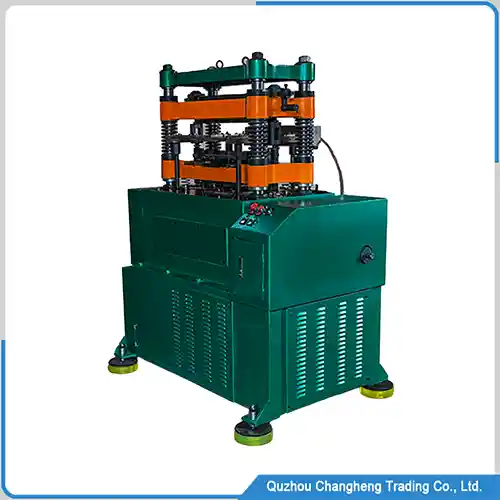

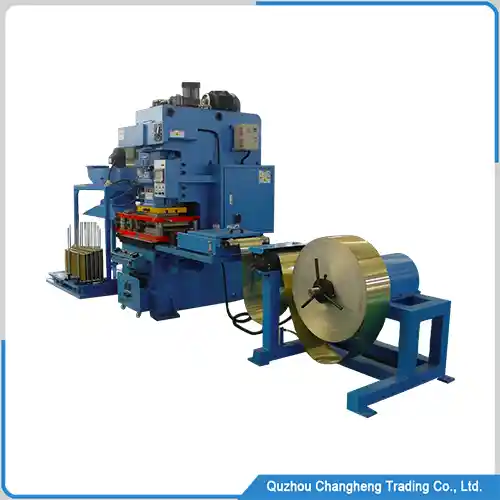
Machine Overview
The Extruded Finning Machine adopts a 3-roller extrusion technology to produce finned tubes, which can ensure strong bonding between fins and tubes and improve heat exchange efficiency.
Machines can usually precisely adjust parameters such as extrusion speed, temperature, and fin spacing to produce finned tubes that meet specific application requirements.
At the same time, the machine’s structural design is stable and durable, able to withstand long-term continuous production, ensuring the equipment’s stability and continuity of production.
The Extruded Finning Machine can produce finned tubes with good thermal conductivity and structural strength, thereby improving the performance of the entire heat exchange system.
In addition, the machine’s design follows international quality standards, such as ISO standards, ensuring the quality and safety of the product.
Extruded Finning Machine data
No. | ITEM | DATA |
1 | Drive Motor Power | 11KW |
2 | Machine Weight | about 1.6T |
3 | Overall Dimension | 245*100*165mm |
4 | Fin Rolling Speed | 0.6 m/min |
5 | Fin Material | Copper aluminum |
6 | Tube Diameter | 7-45mm |
7 | Fin Thickness | 0.2-0.7mm |
8 | Fin Pitch | 1.8-7mm |
9 | Max Fin Height | 7mm |
Working process of extrusion finning machine
- Raw material preparation:
Firstly, the factory needs to prepare the metal tubes, such as aluminum and copper, needs for manufacturing finned tubes.
- Material cutting:
Cut the metal pipe into the required pipe length, and the maximum production length of this machine is 6 meters
- Fin tube forming:
The worker needs to connect two pipes together and put them into the extrusion fin machine’s roller mold. The roller mold will automatically form a fin Tube.
- Surface treatment:
The surface of the form fin tube may have some residual coolant, which needs to be cleaned with a high-pressure water gun to improve its appearance.
All the workflow has been completed here, and precise control and management are required during the production process to ensure the quality and production efficiency of the fin tubes.
Different tube wing machines may have differences in details, but the basic principles and production steps are similar.
Extruded Finning Machine working video
Installation precautions
The installation process of this extruded finning machine is straightforward, and even new workers can complete the installation work. Here are just some precautions
Connect power supply
The power supply of the squeezing fin tube machine is 380V three-phase, which means three wires are needed to connect the motor,
Please note that when connecting the power supply for the first time, it is necessary to check the direction of motor operation. Two wires need to change if the motor runs in the opposite direction.
Gear lubricating oil
Because there cannot be any liquid inside the machine by sea or land, we have drained all the lubricating oil,
When the machine installation is completed, lubricating oil must be added to the gearbox.
Cooling fluid
Our extruded finning Machine has an automatic cooling device, and the coolant can be recycled, but it must use high-quality coolant. We will provide some coolant samples for your reference because extrusion production generates much heat from metal tubes, so a high-quality coolant must be used.
FAQ
A: This machine has no mandatory coolant requirements. You can use any type and brand.
A: An ordinary worker takes approximately 1-2 hours.
A: We provide free installation services, but installing this machine is very simple. You can easily install the machine by checking our installation video and manual.